[ Back ] [ The Roadtechs PetroChem / Fossil / OffShore Job Board ] [ Help ] [Edit ] [Mark Position Closed ]
At PIC Group, Inc., our emphasis is on excellence. We recruit the strongest candidates in the power generation industry. As a global service provider, we continually seek talented individuals.
Title: Shift Supervisor
Position Type: Contract
Location: San Antonio, TX
Reports to: Operations Manager
Status: Non-Exempt
Job Summary:
PIC Group has an immediate opportunity for a Shift Supervisor in a fast paced and dynamic state-of-the-art Research and Development Facility located in San Antonio, TX. The Shift Supervisor would report to the Operations Manager and be responsible for operations of proof-of-concept project that recycles plastic through a cutting-edge catalyst reforming process. The Shift Supervisor is responsible for all plant operations and maintenance activities during his shift, including personnel safety, equipment safety while operating a fluidized catalytic cracking unit (FCC) and other ancillary systems designed to molecularly change plastics into its original form. The Shift Supervisor will play an integral part in developing and maintaining a coordinated approach when directing operations personnel in the start-up, operation, shutdown, and maintenance of the feed and melt system, reactor, regenerator, main column, and all balance of plant equipment.
Essential Duties and Responsibilities:
• Direct shift operations personnel in the safe and efficient operation of the process demonstration unit from inside and outside the control room.
• Direct and oversee shift operations personnel in the proper start-up, operation, and shutdown of equipment, systems, and the plant in accordance with plant procedures.
• Monitor and record plant operating parameters inside the control room; adjust as required to maintain safe and efficient operation of the plant.
• Upon identification of faulty equipment or system operation, troubleshoot the cause and take proper corrective action to restore the plant to a safe condition.
• Respond to system and plant emergencies in accordance with the emergency response plan, and lead shift operations team in the safe response to any emergency.
• Monitor plant air emissions and take steps to maintain within acceptable limits; notify the Operations Manager of situations that may result in violation of established limits and/or regulatory requirements.
• Monitor the activities of maintenance personnel and contractors working in the plant to ensure activities are conducted in a safe and proper manner.
• Verify and authorize isolation and lockout/tagout of plant equipment, as required, to support plant maintenance, testing, and other operational activities.
• Periodically audit the lockout/tagout system to ensure all required tags and locks remain in place, and program is administered properly.
• Prepare shift and Daily Operational Review reports as directed by the Operations Manager.
• Observe and correct situations that may develop into future operational problems or safety hazards.
• Report and direct shift team to respond to chemical spills and leaks in accordance with plant Emergency Response Plan.
• Direct and oversee shift operations personnel in the operation of equipment disconnects, circuit breakers, and switches; as well as all required field operations duties such as catalyst loading, valve operation, sample collection, etc.
• Obtain thorough turnover from Shift Lead being relieved, including special orders and unusual operating conditions.
• Review plant status and operating logs prior to taking over the shift.
• Conduct thorough turnover to the relieving Shift Lead for special orders and unusual operating conditions.
• Schedule and supervise tests on plant fire and chemical safety equipment.
• Identify and authorize work requests for defective plant equipment.
• Supervise shift team to maintain the plant in a clean, orderly condition.
• Schedule and conduct safety meetings and periodic training.
• Assist in training subordinate personnel.
Job Requirements:
• Demonstrated experience in plant unit start-up, operation, and shutdown from inside and outside the control room, using local controls and the Distributive Control System (DCS).
• Proven experience in leading a shift team of operators in the safe execution of plant operations.
• Thorough knowledge of equipment isolation and tagging procedures.
• Experience responding to plant abnormal situations, upsets, alarms, and emergencies.
• Thorough knowledge of the location, purpose, and proper use of the plant safety equipment.
• Specialized training and/or experience in the monitoring and diagnosis of rotating equipment issues.
• Specialized training and/or experience in Environmental Protection, including associated plant systems, equipment, limits, and regulatory reporting requirements.
• Specialized training and/or experience in supervision of emergency response to fire, flooding, bomb threat, chemical spill, oil spill, and fire.
• Specialized training and/or experience in supervision of technical personnel, including cultural relations, race relations, team building, conflict management, and prevention of workplace discrimination.
• Specialized training and/or experience in the evaluation of employee job performance, progression, and compensation.
• Good communication, leadership, teamwork, and presentation skills.
• Strong analytical, problem-solving, and organizational skills.
Physical Requirements:
• Prolonged standing, combined with periods of walking the plant floor multiple times in a shift.
• Ability to reach, climb, stoop, and lift to 75 pounds.
• Ability to identify warning alarms and distinguish between them.
• Able to tolerate the day-to-day sounds of an active plant setting.
Education / Experience:
• High school diploma required.
• 2 years advanced education in an Engineering or relevant technical discipline or equivalent combination of training and experience required
• 5+ years as a Shift Supervisor in a plant setting
• 10+ Experience in chemical/petrochemical plant start-up, operation, and shutdown from inside and outside the control room, using local controls and hands on time running the Distributive Control System (DCS)
PIC Group, Inc. is an Equal Opportunity Employer. We offer competitive wages and benefits. We seek out and employ talented individuals who meet the qualifications for each position. Due to the large number of responses we receive to our postings, only those applicants with the required experience and qualifications will be contacted.
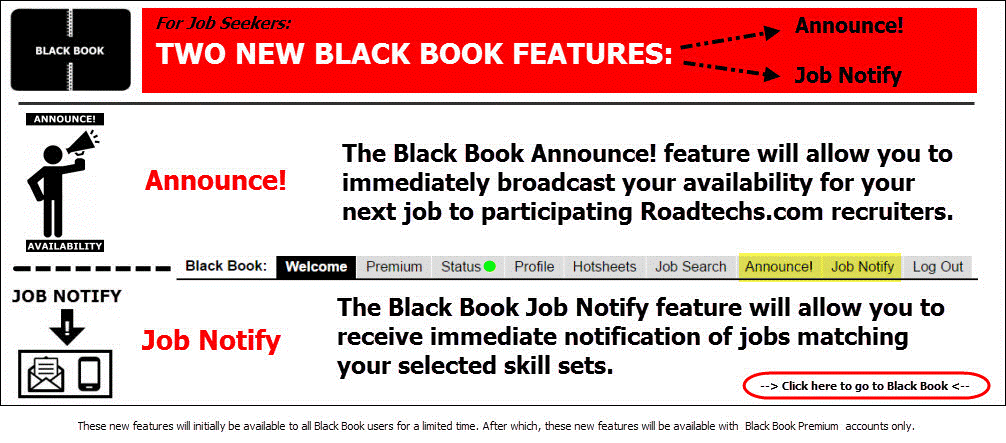
© Copyright - Roadtechs®, LLC. - All rights reserved.
Use of the Roadtechs.com website implies compliance with the Roadtechs User
Agreement and acknowledgment of our Privacy Policy.